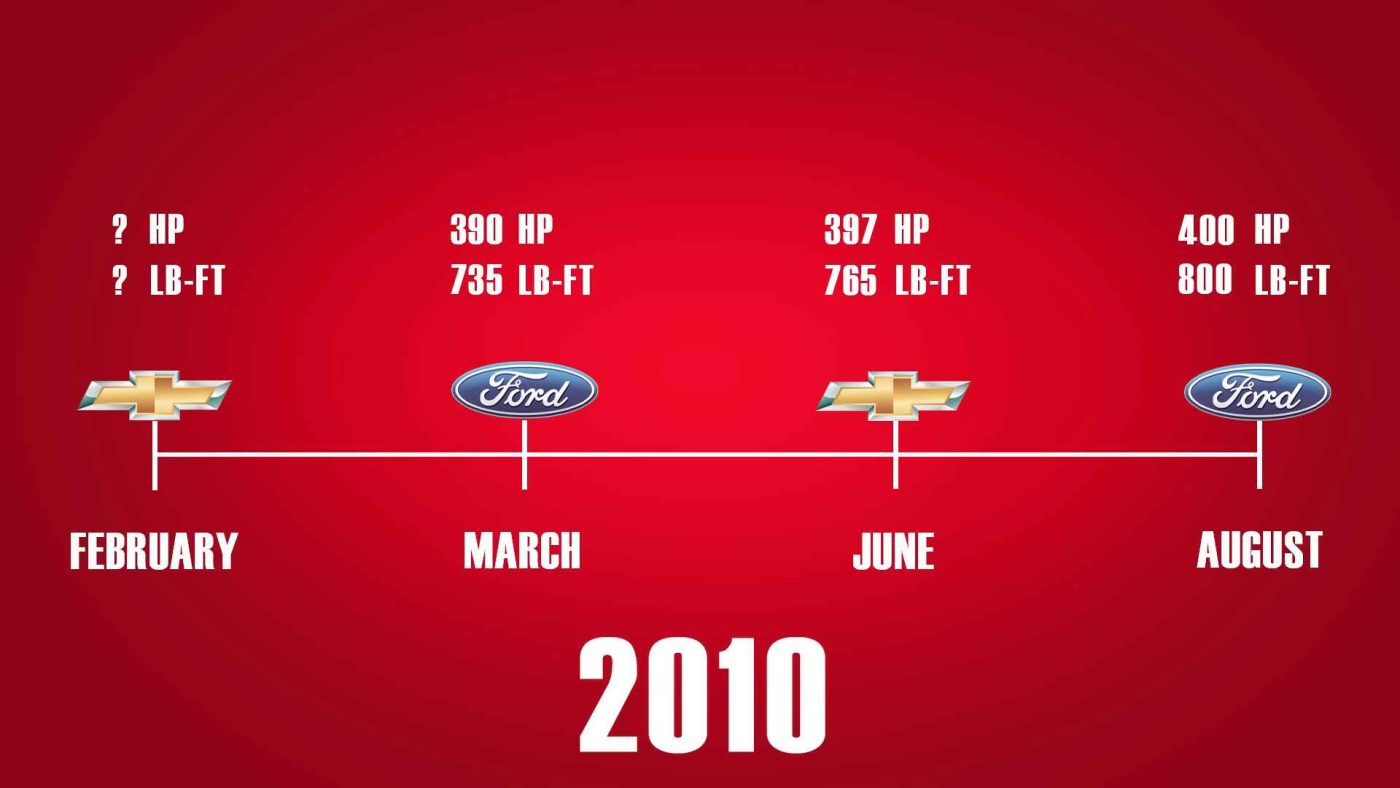
Ford is winning the horsepower war and I want to know how so I want to have a look inside and find out what is it they’re doing we’re going to take apart this 2011 scorpion engine that Ford sent me in 2010, and it’s been on this stand Ever since Mike it’s time to blow a Ford apart, I’m Gail Banks. You may not know this, but I’ve been hot rotting Ford since 1956. When my dad asked me, hey Gail, go out there and put a new head gasket on your mom’s Model, A it’s the last time she ever saw that car. Today, I’m going to talk to you about a 6.7 L Ford diesel engine known as the Scorpion.
This engine was quite a participant in the ongoing horsepower Wars between the big three, while I’m interested in the current horsepower war between Ford and Duramax. This isn’t the first horsepower war between these two engine types. That’S ever existed, the original one and somewhat unknown. One took place in 2011 and late 2010. It had to do with Peak horsepower and Peak torque to be claimed on their respective 2011 models.
In February of 2010 GM announces the new Duramax powered Silverado, but does not reveal the horsepower and torque kind of waiting till Ford tips, their hat in March of 2010, one month later, Ford announces a best-in-class 390 horsepower at 2800 RPM and 735 pound feet of torque. At 1600 RPM now it’s kind of crickets for a while uh Fords put their cards on the table. But then, in June GM announces the Duramax will have 397 horsepower, beats them by seven and 765 PB feet of tur beating their 735. But Ford had certified two power ratings with EPA and carb. In other words, they had a smog legal whole card, so not in July, but in August of 2010 Ford announces an upgrade to 400 horsepower and 800 pound feet of torque whoa.
First horsepower War Ford prevails when Ford first announced their early numbers. You can look at the horsepower and torque curves that they published at the time and see the torque curve just goes flat on top and to some extent that impacted a little flatness on the horsepower curve. Look at this, they just lopped off the top of the curve. When I saw this back in the day, I thought oh, that’s dirty they’re going to come and get GM and sure as hell they did. Here’S the updated Dino chart the curves look like they’re supposed to so why am I looking at this engine?

Well, first of all, I have a brand new one and secondly, this is the OG scorpion that started this whole thing between them and Duramax. There’S a number of things that intrigue me about this engine. The first is it’s, what’s called a hot V, the intake ports are not in the Valley of the engine. The turbocharger resides there. The turbocharger resides in the Valley of the Duramax as well, but what’s different here is the exhaust manifolds are in the valley, not the intake manifolds.
So let me take you through the air intake path. This has to be the craziest casting I’ve ever seen. There’S so much going on inside one piece of aluminum, this oval shaped or elliptical shaped Inlet, hopefully, is fed by A banks. Ram air intake system, cold air intake system into here. So here’s air in going to the turbocharger here’s the turbocharger notice, the turbocharger – has a normal compressor Inlet, and it has this this other guy going on here.
So there something strange going on here, we’ll come back to this. Let me take you through here into this. Casting out to the top of the turbocharger and the normal position on the turbocharger, through the compressor and I’ll tip it to you, there’s two compressors in here we’ll get back to that off to the charge air cooler which sits on the inner fender. Well, now, to make all this stuff work work inside the truck, it’s my memory that Ford actually moved the in inner Fender Wells out. They had 8 in more width inside the engine bay to deal with all this, they put a liquid coupled charge, air cooler on the fenderwell, so the Boost air goes over to the charge.
Air cooler returns from the charge air cooler and into this throttle, so that throttle exists for EGR purposes and oh by the way. There’S another Passage to take the cooled. Exhaust gas Reser gases into here and blow it into the intake air inside this tube looks like a mushroom or an umbrella. The EGR is blown into the underside of that umbrella and blown back into the flow kind of mixing it a bit. So the Boost air enters here through the throttle into the EGR mix EG goes in here goes through that section and down into this sink trap, looking thing and up here into the intake manifold, so the boost a from that intake casting flows upward into this intake Manifold splits up here and flows down into each valve cover yeah valve cover.
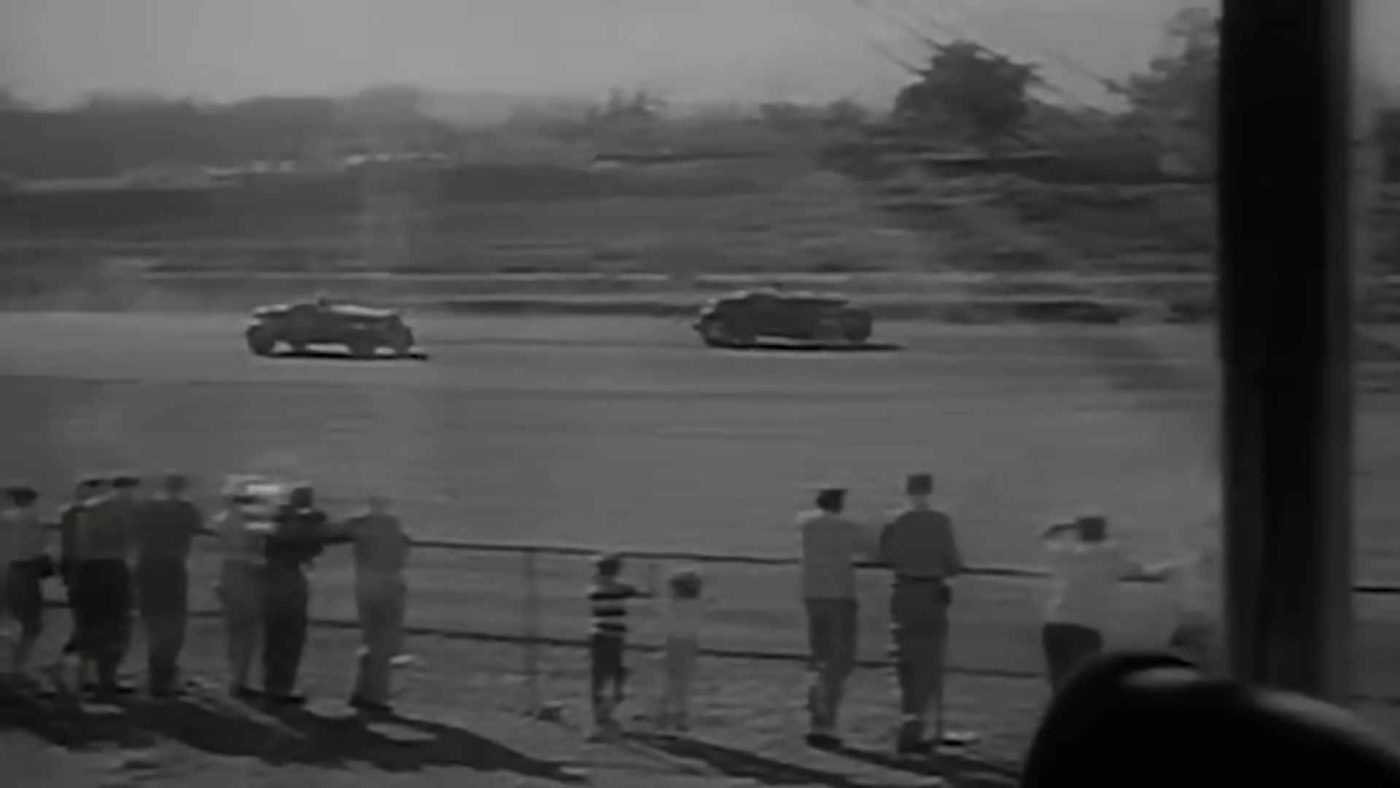
The valve cover is the continuation of the intake manifold and the intake ports are on the outside of the head, so this is radically different to anything you’ve seen before. If you’ve never experienced a Ford Scorpion or a similar hot V engine, now, a lot of hot V engines. I’Ve seen including some prototypes uh that never made production have manifolds on the outside intake manifolds on the outside of the head, and they don’t run the Boost. Air through the valve cover there’s a lot of volume here, there’s a lot of volume in the casting we just looked at and then you’ve got the volume in the charge, air cooler on the fender well and the tube back to that casting through the throttle. Egr mix Etc.
Up into here, the volume of the manifolds, the volume of the valve covers and the volume of the intake ports. You got to fill all of this with boost pressure before the engine responds before you can put fuel enrichment in you, don’t want a rich bump till the air gets there. You don’t want to smoke bump either. There’S always this question: is the hot via really an advantage or not well with a hot V. You’Ve got exhaust manifolds out here here.
You can see one of the exhaust manifolds still boled to this cylinder head and there’s a flange here that feeds EGR into the EGR system. That being the case, you got a lot of heat to deal with in here. That’S right, underneath the intake manifold you’ve got radiant heat from the inside of the engine, the oil Etc. On the valve train heating, the casting it’s all negative, it’s a lot of volume. The shorter intake tract is something I would prefer you know, I’m just talking.
My preferences here, I kind of like the charge air cooler liquid coupled built into the intake manifold in the valley uh, which really shortens up the inlet tract and then you’ve got exhaust manifolds either way you got to fill them with manifold pressure to drive the turbine Anyhow, so yeah you don’t have up pipes, but the intake tract here is pretty profound, so you got to take one delay versus the other. I don’t know if anybody’s ever proved it uh there whether or not there’s an advantage either way. But let’s look at this cuz. This is quite unique all right! So now you get a better look into the intake manifold, that’s built into the valve cover.

This is the entry point, take the valve cover off and we’ll be able to see a little bit more from the underside and get our first Peak at the valve gear looks like I know what I might be doing. The ports are on the outside of the valve c. You can see the uh image of them here and here you’re coming into the ports on the cylinder head and they’ve kicked to the side here. This is really interesting. The directing the intake gases to the side.
So if we look at this properly, so it’s kicking the gases this way into the ports. That’S interesting, because these are the intake valves here here here and here so as you’re kicking the gases. This way, you’re adding some swirl torque when those valves open clever, these guys thought of everything, but the thing that’s the most remarkable is there’s four rocker arms and four push rods on every cylinder I mean this is this is something special. These guys came up with a system where, in there is not two rockers and four Valves and a lot of those have drawbacks to them. When you pull the valve cover off it suddenly whoa, where did this come from?
The rocker arms are sheet steel, they’re, like Stamped Out of steel plate and then they’re formed for push rod cup and a rocker arm face on this steel. Stamping somebody got real clever here. There’S a ball pivot, underneath we’ll look a little more detail here in a second, but basically, you’ve got four rockers, but you’ve only got two lifters you’ve only got two cames and four rockers. This replaces a somewhat problematic thing: that’s decades old and that’s where you’ve got four valves, two rocker arms and to push both valves open both intakes with one rocker or both exhaust with one rocker. You got to have some sort of a bridge piece that it The Rocker pushes down on the bridge piece and it in turn pushes down on two valves.
The thing I don’t like about that is if the Val valve springs are not equally matched when The Rocker pushes down the softer. One go goes down and leads the one with a stronger spring. So when we race like a Duramax, we Precision match the springs and not just the spring pressure, but the open pressure, the seat pressure and the spring rate in between. So we know they’ll progress evenly. I bring the Pistons a lot closer to the valves, so to speak.
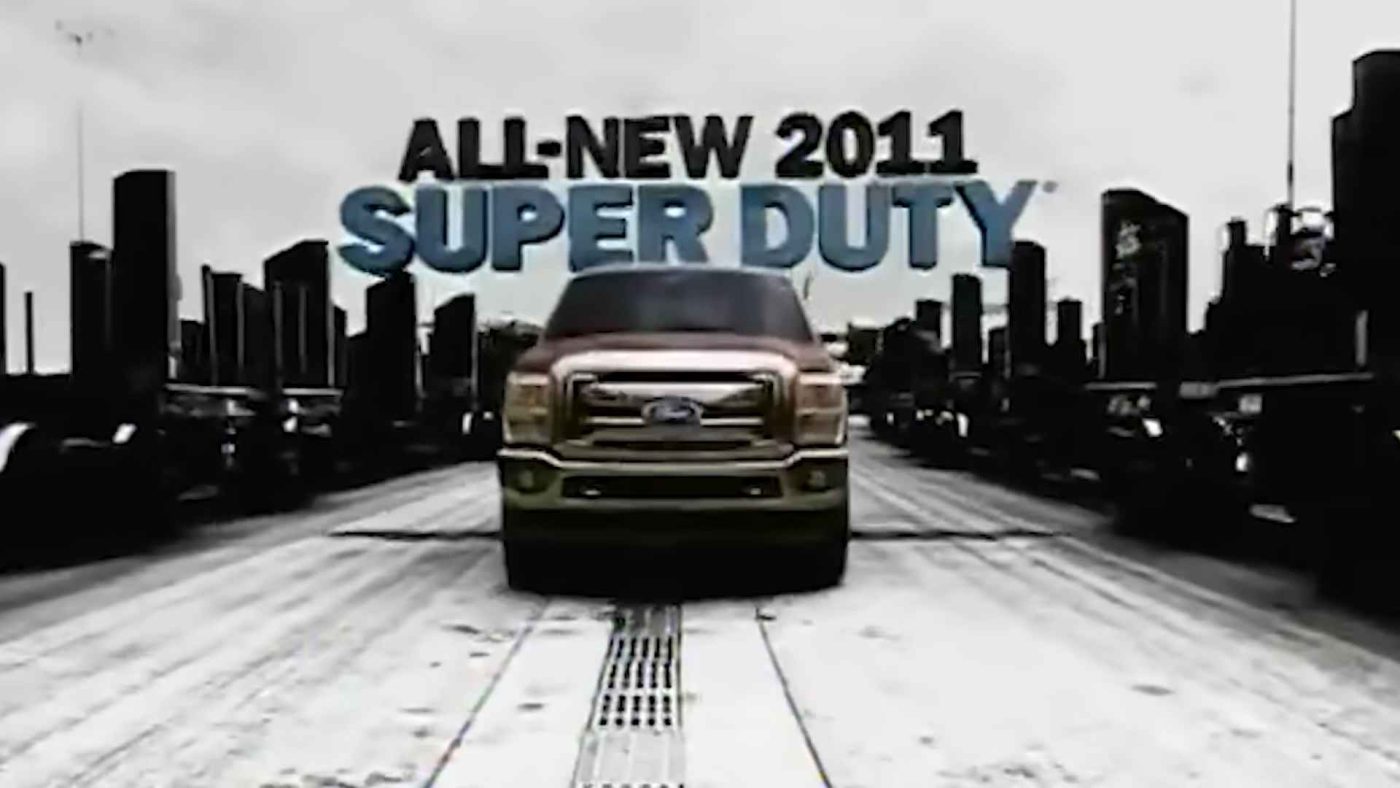
How do I do that higher valve lift uh and when I open them relate related to where the Piston is in the boore at the time, so without getting getting too uh deep into that? These guys have solved it they’ve solved that cros, head or rocker Bridge or whatever term you want to use. I think we need to go back to the table and talk about this, but one feature I want to point out here is how they lubricate all this. This is a spray bar. It has four Outlet very microscopically small Outlets delivering oil into this friction system, one for each rocker, so it’s lubing the push rod to rocker The Rocker to valve the pivot of The Rocker, underneath this bridge and there’s also a slop mechanism.
Here that holds the rocker up against the pivot appears it’s blued. It appears to be a spring steel mechanism, so here’s a cylinder worth of valve gear, including the roller taets. Quite a large diameter roller uh needle bearings inside so they’re, pretty high llama they’re, guided through this cassette that prevents them from rotating in their boore and sliding sideways on the camlo. What’S kind of cool about these and Ford has a patent on this there’s two hydraulic lash adjusters inside each one of these rollers, these little guys they’re, not very big. They insert into the roller with the ball tip up, they drop in, and this is a zerol lash hydraulic system.
So you never have to lash this. The push rod goes in with a cup down, which is highly unusual in rocker, arm systems and ball up, and there are four push rods: two lifters and four rockers. These Rockers are sheet steel, how the hell they form the various components on The Rocker, starting with the friction face for the top of the valve. You’Ve got to have a beautiful radius, the right alloy, the right hardness to go a half a million miles or more, it looks like, and if, if this is true, it looks like these shapes this. The ball pivot for The Rocker and the push rod cup.
For the push, rod all appear to be formed out of the parent metal of this stamped piece. If so, these guys are geniuses, I mean it’s a fabrication Miracle. Tell you the truth. There you got it two lifters four push rods: hydraulically, adjusted and four stamp Steel. Rocker arms – and they run this up.
Probably the limiting speed is well above 32. 3,300 RPM. I know the horsepower Peak on the 2011 engine is at 2800 RPM the horsepower Peak on the current engine, the one that’s really the badass 500 horse 1200 PB foot engine that horsepower Peaks at 2600, a little little slower, but a lot has happened between 2011 and 2024, but don’t worry we’ll get to the 2024 engine. So if you think this valve gear is interesting, wait till you see this turbo all right. So this is the Garrett dual boost: VNT waste, gated, dual compressor on a common shaft turbocharger.
I don’t know what they left out: uh ceramic ball, bearing. Let me take you through this baby, I’m going to start on the hot side, because one of the advantages of hot V is you get the exhaust energy right to the turbine wheel. Right, I mean that’s what everybody says is the advantage. You got exhaust manifolds conventionally on the outside of the cylinder heads you have pipes that lead up to the turbocharger Inlet on the AFT end of the engine. Now I’ve seen it tried different ways.
In this case, you didn’t get rid of. If you will the up pipes here, they they are so you’ve got two pipes with Bellows to align any misalignment uh which Al oh yeah, they streamline them. That’S nice uh put a sleeve inside, but the inside diameter of all of this stuff. In fact, the inside diameter. Here’S one of the exhaust manifolds the inside diameter of this exhaust manifold out is incredibly small they’re keeping the velocity up.
So you can kick an kick. The turbine in the ass more readily, but you trade that velocity for drag and back pressure versus this, the small size. So there’s always a tradeoff uh somewhere, I’m quite an advocate of higher cross-section and solve your response problems elsewhere, and then they introduce into the turbine housing which houses a VNT section, what they call variable, nozzle turbine the ows you to vary. If you will the flow onto the turbine wheel to speed it up or slow it down, but just in case that didn’t work sufficiently, they also threw in some old school and there’s a waste gate. Here’S the the arm to actuate the gate inside the housing and here’s the diaphragm, which, oh by the way, is vacuum, operated uh.
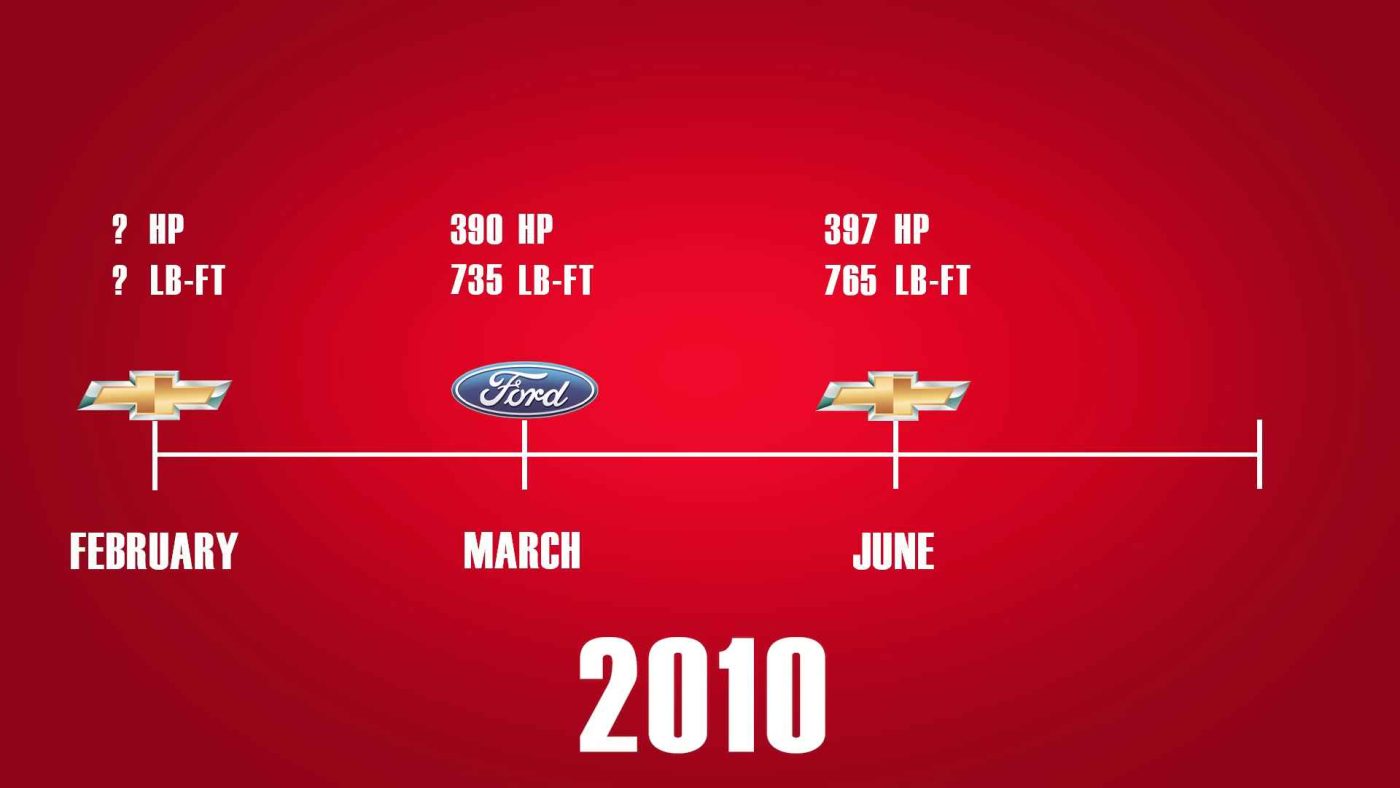
You don’t, naturally get vacuum on a diesel engine uh. So there’s a mechanically driven vacuum pump, hiding Elsewhere on this engine, to drive something like this vacuum: actuated waste gate, so you’ve got two boost control systems on the same turbocharger, so you got to get the shaft speed kicked in the ass up to speed before you Get compressor RPM sufficient to make things happen, and this it’s this compressor. I really want to show you remember: we have two inlets into the turbocharger, the con on Center Inlet and this other Inlet that goes to what would be the back plate behind the compressor wheel. So if we take off the compressor housing, it becomes apparent, they’ve got some anti- surge technology in this compressor cover, which appears to be uh, acting, probably the most effectively on what is the front wheel. But what we have here and it’s very difficult to see the back back wheel, but on a common shaft, we have a compressor wheel with two faces and two sets of veins or or fins whatever term you like using on a common shaft.
The blade count looks to be very similar. I can’t see that much of the rear, except in this cutaway, that we’re showing you on screen and then it’s pretty obvious what’s going on and we seem to have some anti- surge technology also on the back back compressor. Impeller, what we’ve also got is a from the front bearing in the in the bearing housing to the tip of the shaft is inordinately long and there’s much more mass on there. Almost the mass of two compressor Wheels. The whole idea here was to have this work at low boost pressure, low shaft, speed, low mass flow, all the way up to high boost pressure, lots of dens production and therefore lots of mass flow per CFM.
It’S all out here. It’S like a popsicle on a stick. You’Ve got all this Mass dangling out on this shaft, so they put these ceramic bearings in here because back then that was the hot lick. Everybody was going to ceramic bearings for better response. They did test at G, ball, bearings versus plane, bearings and low mass rotating group versus conventional Mass rotating group, and they found that the mass of the turban, impeller, shaft and compressor impeller was more meaningful to turbocharger response than the bearing system.
In other words, if you, if you use the same bearing system in both cases and, of course, guys, hey spin, this – you know you’ve been at a trade show, they grab the shaft, they spin it. It keeps spinning ball, bearings, they’re, dried now, spin, the plane bearing you, spend the plane bearing it’s dry. Well, that’s not how they run the plane, bearing runs with an oil film. So the shaft is not touching. The plain bearing like it is on the bench and or the display at the show and the ball bearings are interfered with with lubricant gumming up their rotation, so this stuff on the table spin, the thing uh-uh.
So when you do it on the gas stand and you put the exhaust energy to it and you’ve got a compressor load and there’s virtually no difference, then why are you paying for the ball? Bearings man’s got to ask in this case this Canever load. They started this in 2011 production through 2012 they’re having lots of bearing warranties compressor on a stick. So they went to steal ball bearings for the next 2 years and by 2015 they had discontinued the whole turbocharger. I can’t imagine the amount of money they spent on design bugging this out over a period of years, tooling it producing it only to have it gone in four years.
There is one thing that I really like here: uh, it’s something I’ve been doing uh most of my career and it’s this exhaust Outlet mounts on the turban housing see the shape. Cobra head is a term the guys at Ford use for this, and this is double cool. By that I mean it’s cool because of its shape. This is called NAA, duct NACA National advisory committee for Aeronautics. It’S a government agency started in 1915 was disbanded in 1958, but these guys sought a World War.
I fight aircraft all all the way through the Bell. X1 breaking the sound barrier. Naa had to do with it, but I like this because it’s the lowest loss way of making a tight 90 Bend. This one in particular, has a chamber between the inner and outer section, which also provides kind of an air barrier type of heat shield between this and the firewall in the truck and for my closing act, I want to show you one serious oil pan casting this Thing you know you talk about that air intake piece with all the passages in it. This is the second really complex casting on this engine.
Let me take you through the oil flow. It’S pretty damn cool oil pickup in the bottom of the pan feeds from the bottom of the pan into the oil pump. The oil pump said gerotor, which is frankly my preferred design of oil pump. There’S some some pressure regulation that goes on up here, uh at the front of the cylinder case, so the oil comes out of that gerotor pump into this bore and there’s a cast in oil tube that feeds it inside the oil pan into the oil cooler out Of the oil cooler across once again inside the oil pan to the oil filter out of the oil filter and then up here and into the engine into the block and consequently to the heads all the lubricating chores are fed by that hole. Turbocharger everything.
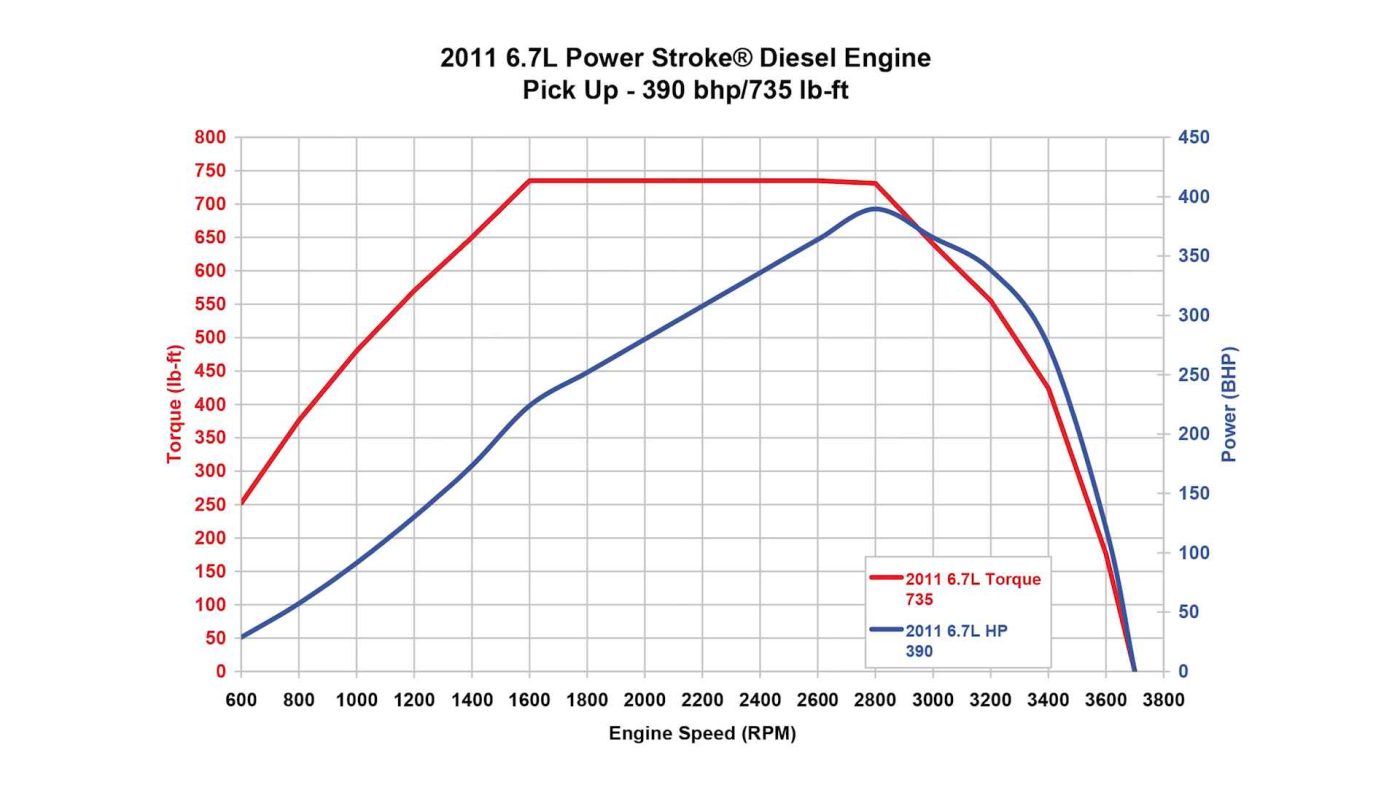
So I want you to know these guys weren’t, slacking, structurally or thermally. Back in 2011, we’ve got a compacted graphite block, which is current technology uh and my preferred block casting alloy. We’Ve got six bolt Maines four down and two side uh, so you got side bolted. Four bolt Mains: if you want we’ve, got a forge steel. Crankshaft we’ve got rod, bearings, which are tangless, there’s no Tang uh to guide them side to side and there’s an upper and lower identified by the dark upper and the bright lower same with the main bearings.
So when you’re assembling the engine, you know which bearing goes where the rods are forged powder – cracked cap rods, so so the alignment of the cap once you’ve machined the rod you take it apart, clean it put the bearings and wrench it back together. It is absolutely perfectly aligned every time unless, of course, you put the wrong cap on the wrong Rod. Then it’s chaos uh, the Pistons are Gallery cooled uh, so there’s cooling nozzles down in the block and you can just C catch one. Looking up the boore at us, if you look down the boore, there’s an oil gallery inside the Piston crown that cools the Piston with engine oil. So this is the granddaddy of the Scorpion, that’s winning the horsepower Wars today.I can’t wait to get my hands on one of those 24s hey Mike. Can you put this engine back together? For me,